I just finished fire polishing the second batch this morning. Overall this second batch turned out pretty much the same as the first even with a more “Bunny” firing schedule.
Here’s the second batch ready to be fused.

Here’s the schedule I used.
RAMP | TARGET TEMP | HOLD |
100 | 900 | 30 |
200 | 1250 | 30 |
FULL | 1480 | 15 |
FULL | 960 | 60 |
75 | 800 | 45 |
100 | 700 | 0 |
200 | 200 | 0 |
With the slower ramp up the clear marbles didn’t shatter like the last batch but I still had internal cracking like the last time.

The orange marbles also cracked like crazy.


All the other marbles were stable but they either didn’t fire polish well or the patterns where just uninteresting. Here’s the remaining batch before the fire polish.

After the fire polish.

Here are the results close up.
The blue marbles contained a whiteish glass that just would not fire polish.

The red marbles polished OK but for the most part uninteresting and extremely brittle. I had a cordless phone standing on the bench next to one when it tipped over on to one of them and shattered it.

The orange ones came out the best but weren’t necessarily that interesting.
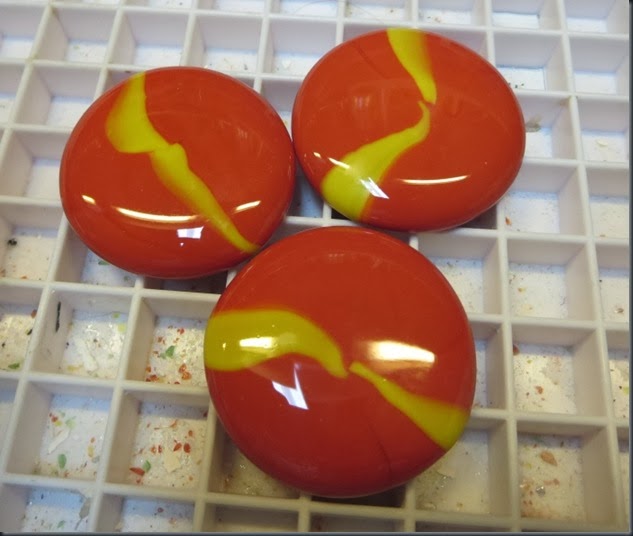
These might be good for making bolo ties. I don’t know. I got to think about it some more. I was talking with Marcia (my wife) tonight and she remembered co-worker that has tried fusing marbles saying she got them at Goodwill and that they were older marbles (ca. 1970s). It’s possible that the chemical composition of the older glass is more fuse friendly. I’ll have to check it out sometime.
Cheers.
Blogger Labels:
Marbles,
glass