OK. The title’s a bit over dramatic but this has been good learning experience. In my last pot melt post I mentioned that I was going to add a white border to the melt to make a blank for a plate.
Well here’s how things went down.
I used a 10 inch stainless steel ring to contain the border.


I used Uroboros COE 96 opal white coarse frit.
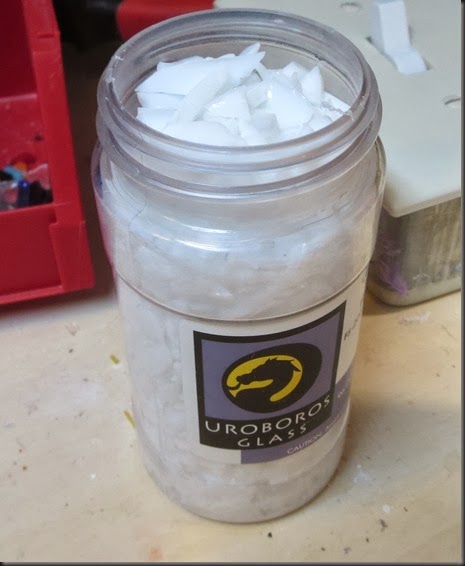
Here’s the melt with the frit poured in. I used a pot melt calculator to figure out how much frit I would need. If you look closely you can seed the edges of the melt are a bit ragged. I did some grinding but I made the assumption that the full fuse would, well, kind of fix everything.

Well, not really.
The white filled in where there were nicks along the edges. In addition the melt is slightly off center. I was able to fix some of that through grinding but the melt still isn’t quite where it ought to be. I figure I should have taken the melt to a full fuse in order to smooth out the edges of the melt. The reason why I didn’t do a full fuse is that there was no pig tail to remove so I figured that was a step I could skip. I think if I had taken the melt to full fuse the edge would be a smoother. I think also I’ll use fine frit to make the border. Another way I’ve heard of doing a border is to set the melt on a 3mm circle of white and doing a full fuse. That’s something I’ll have to try for a future melt.

Another downer is that it looks like a piece of kiln led fell off during the fuse and into the glass. I’m kind of kicking myself now but I’m thinking I could have taken and awl or a finishing nail, dug the fragment out, fill the void with frit and fused it again.

Here’s the slumping mold I used.

And here’s the final result.


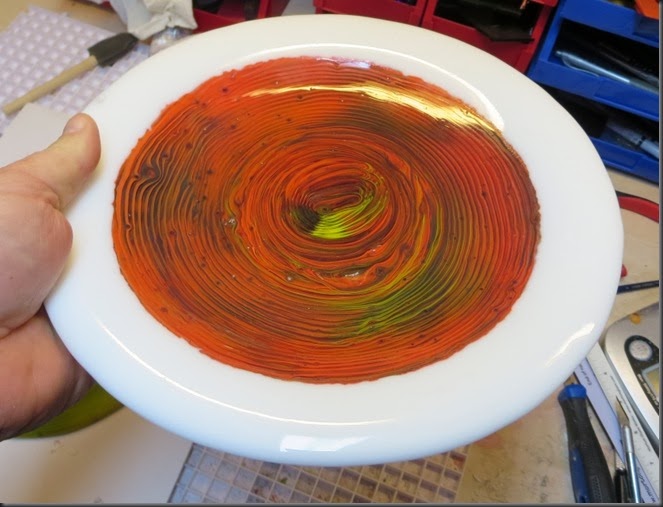
So my goals for the next plate I make are:
- Clean up the ragged boundary between the melt and the border
- Spend more time making sure the melt is centered
- Spend some time inspecting the kiln lid for loose fragments of fire brick.
I looking forward to doing the next plate. I did a full fuse on a melt I did earlier to get rid of the pig tail and (of course) the edges of the melt are much smoother.
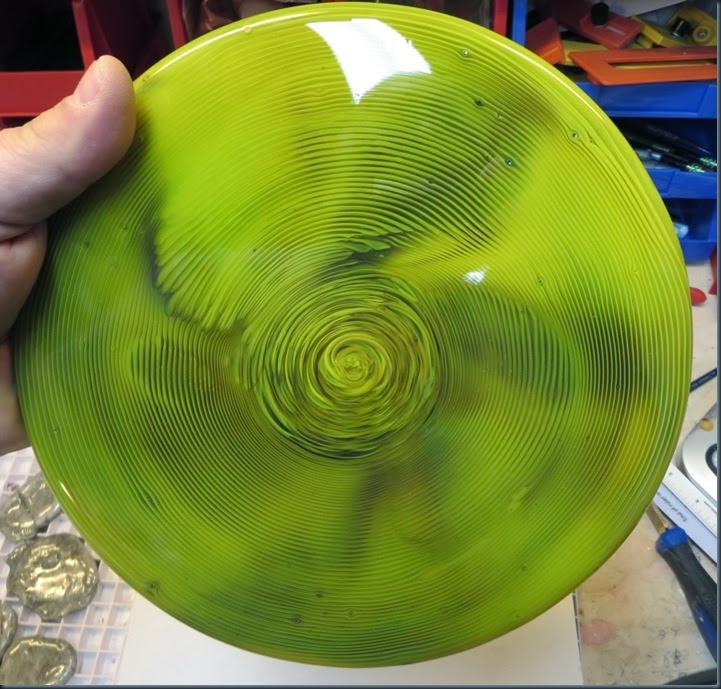
On another note it seems to me that COE 96 glass plays a lot nicer (at least in pot melts) than COE 90. For example this melt was close to 8mm thick and did not seem to have any problems spreading out to 6mm after a 20 minute fuse. My first pot melt was done using COE 90 and I could never get it to spread out to 6mm. It’s possible that I didn’t have the kiln hot enough.
Cya!
Blogger Labels:
Pot Melt,
Uroboros,
fire brick,
frit