First Shenanigan
So what do you do when you have several empty olive jars?

You try fusing them together just for the hell of it.

Well not totally…I had visions of making a blank out of them and then slump it it into a mold for some kind of snack bowl. I remember seeing a mold over at the Delphi Glass that looked like it would be the right size (about 6.5 X 9). The results of the fuse leave a bit to be desired.

It sort of looks cool but it suffered some major thermal shock on the cool down because of the uneven thickness of glass and a cooling schedule that was too aggressive.

I needed to use a more conservative cool down schedule plus I probably should have fused it longer at 1500 degrees to flatten it out a bit more. I held for 15 minutes when I should have done 30. It’s back in the kiln again to see if I can fix it.
Second Shenanigan

I talked about this melt in a blog post a couple of months ago. I won’t rehash the details here but I’ve been trying to think of ways getting it back to the shape it was originally intended to be: round. I decided to try a method I had been using on my other pot melts to expand the size of the melt and give it a little border. When I do a pot melt I create a blank in a Slumpy’s 8 inch mini melt and then flatten it out by taking it up to 1500 for 45 minutes. I end up with a melt that’s about 10.5 inches in diameter. I found I can expand it out to about 12 inches by cutting out a clear 11.5 inch circle of glass, putting the flattened melt on top and then fusing them together. I end up with a melt about 12 inches in diameter which fits perfectly in the 12 inch melt stand.

Anyway I decided to try this technique to get the oblong melt back into shape.

I traced around my piece with a marker and then cut it out.

I had to use some etch to get rid of some kiln wash that had stubbornly baked on the back of the glass. Either it’s my wash that’s causing that problem or else it may be one of the downsides to melting directly into a form.

I then put the two pieces in a 12 inch ring casting mold; the clear glass on the bottom and the melt on top. My thinking was that the mold would confine and glass and force it to fill out the circle. It worked pretty darn good. I still had do do some grinding but for the most part I ended up with something that was reasonably round.
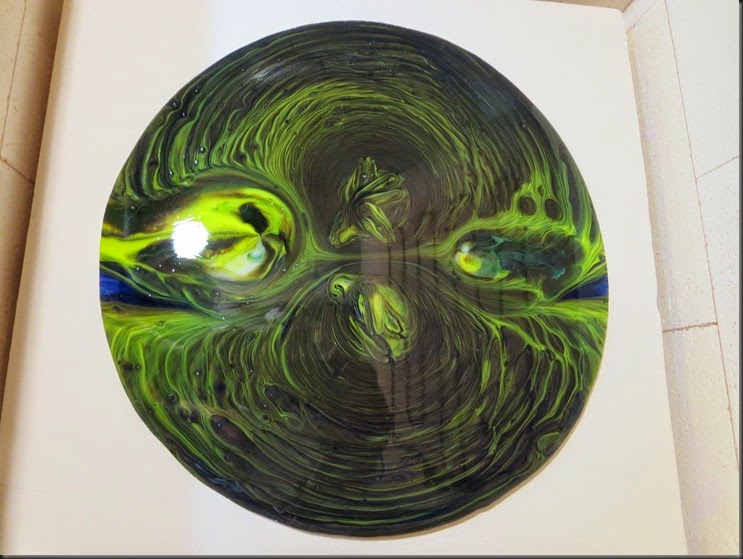
Third Shenanigan
A touch of tragedy here. I had this decorative plate that I had made that I really didn’t care about. It was kind of lopsided and just didn’t come out like I expected.

I had it in storage and there was another plate on top of it. They were separated by a couple of pieces of paper towel. So it really didn’t break my heart when I found it had broken into two pieces when I checked on it. I tried to salvage it by fusing it together again. It came out “OK” (still wasn’t crazy about it). I put the blank back on the rack to slump it some other day. The next day my wife was doing the laundry when she heard a CRACK followed by a CRASH. The piece had split and half of it fell of the shelf and on to the floor. I decided to cut it up and use some pieces in pendants but then I got the Idea that maybe I could resurrect some of it as a mosaic type thingy. So I took my cut up pieces, some additional clear glass and a large blob I got from a batch of blown glass scrap off of EBay. I figured the blob would make an interesting center to the piece.
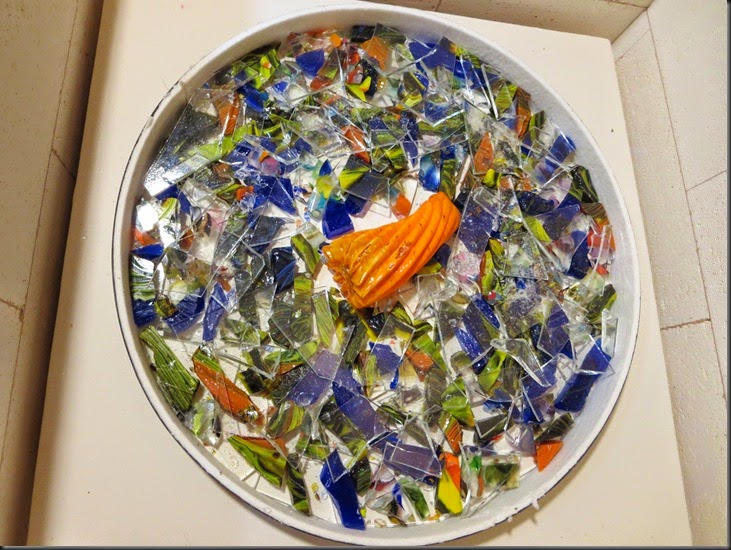
I’m not sure which I the more; this new incarnation or the original piece. You decide for yourself.

Unfortunately (or maybe hallelujah) this piece is no longer among the living. you see on thing I didn’t take into account was that the massive piece of glass in the middle made the blank about 1.5 millimeters thicker than the edges and so my cooling schedule wasn’t conservative enough and this beastie was in two pieces again after 24 hours. I tried fusing it back together again with a more conservative cool down schedule but it still wasn’t enough. It was in two pieces again when I opened the kiln. It’s now resting comfortably in file 13.
End of Shenanigans